Euskadi, sede fabril de los aviones y automóviles del futuro
Los nuevos materiales ayudarána reducirel peso y el consumo
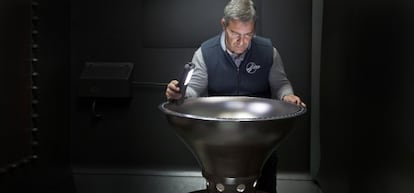
La industria de Euskadi está implicada en el respeto al medioambiente, desde la constatación de que es prácticamente imposible el vertido cero en las fábricas. Pero las empresas fabriles vascas, sobre todo los productores de componentes para los sectores aeronáutico y de automoción, se están esmerando en aportar unas piezas más sostenibles en los coches y aeronaves del futuro.
El objetivo es reducir peso y ruidos, además de emisiones de CO2 a la atmósfera, pero sin rebajar los niveles de seguridad en el transporte de personas y mercancías.
Con este reto, el complejo tecnológico Automotive Intelligence Center (AIC) de Amorebieta (Bizkaia), donde las compañías vascas mejoran los desarrollos relacionados con la industria de las cuatro ruedas, celebró el pasado 8 de noviembre un encuentro sobre los nuevos multimateriales que ahora se utilizan en pequeñas series en el ensamblaje de vehículos.
En la jornada participaron expertos de seis países que trabajan en marcas automovilísticas, proveedores de primer nivel y centros tecnológicos.
Para dar ambiente, en el hall de entrada de AIC se expuso un modelo BMW Serie 7. Mejor dicho, dos unidades. Una entró rodando al edificio y la otra estaba totalmente desmontada, con todos sus componentes y estructuras escrupulosamente alineados sobre una serie de mesas. Vamos, como un supermercado del automóvil. El responsable de esta espectacular deconstrucción de un coche fue la empresa francesa A2Mac1.
Mikel Lorente, técnico de AIC, abrió el evento declarando que la reducción de emisiones de gases de los coches, que son culpables en parte del cambio climático, puede conseguirse mejorando los niveles de eficiencia energética en esta industria. Y los nuevos materiales son una de las claves para conseguir esta mejora.
Lorente habló del aluminio y de la fibra de carbono, entre otras opciones, como el magnesio y los polímeros. Comentó que la marca Audi ensaya un uso más intensivo de la fibra de vidrio en el ensamblaje del modelo A6.
Fabio D’Aiuto, responsable del departamento de materiales mecánicos de Fiat, analizó en la jornada de AIClas posibles combinaciones entre el acero y el aluminio, más ligero que el anterior, para la construcción de vehículos. Su departamento trabaja en una dimensión virtual de los posibles desarrollos.
En el ordenador, D’Aiuto y su equipo comprueban que el magnesio pesa una quinta parte menos que los materiales convencionales, sin perder su condición de alta resistencia. La mayoría de los vehículos pesan más de una tonelada. Las estructuras de acero aportan la mayoría de esa grasa, en torno a los 800 kilos. Por tanto, este es el núcleo sobre el que hay que actuar con los nuevos materiales y procesos de ensamblaje innovadores, entre otros avances.
Según los cálculos de Fabio D’Aiuto, por cada kilo de menos en una estructura de acero, las marcas se ahorran dos euros en el proceso de producción. Multipliquen, por ejemplo en el caso de la fábrica de Mercedes-Benz en Vitoria, que este año aspira a una producción récord de 137.000 unidades de sus modelos Vito y Clase V, cada uno de los cuales pesan bastante más que una tonelada.
Con el aluminio, y siempre según los números de Fabio D’Aiuto, ese kilo de menos supondría una economía de hasta cuatro euros. Cinco euros si se trata del todoterreno Jeep Renegade, que con los nuevos procesos pudiera reducir su peso hasta en un 35%. En otras marcas, como Maserati, el aluminio ya tiene más peso en el conjunto del vehículo que el acero.
La participación de Mervyn Edwards, del centro tecnológico británico TRL, en el acto de AICestuvo centrada en los niveles de seguridad del vehículo eléctrico, una solución para eliminar el consumo de combustibles que no termina de arrancar por la falta de planes para una red de recarga de baterías. El petróleo en precios mínimos, en la banda de los 50 dólares por barril, cuando ha duplicado sobradamente este precio, tampoco ayuda a impulsar las matriculaciones de unidades alimentadas por baterías.
- Aeronáutica
Con respecto a la aeronáutica, la industria vasca de componentes está implicada en el programa Clean Sky de la UE, que quiere que Airbus construya aviones más respetuosos con el medioambiente, con menos emisiones y ruidos. Desde luego, la contaminación directa en el cielo tiene que ser mucho más nociva que la terrestre para la sostenibilidad del planeta, sostienen algunas voces. Aernnova participa en la segunda parte del programa Clean Sky como agente dinamizador de inversiones que suman 70 millones. En su planta de Berantevilla (Álava) ha construido la primera de las alas inteligentes que equiparán el nuevo A340. La estructura partió este año desde Berantevilla con destino al aeropuerto de Tarbes (Francia), donde Airbus continuará con los ensayos.
La estructura desarrollada por Aernnova reduce en un 5% la resistencia aerodinámica de las alas convencionales, con lo que eso supone de ahorro de combustible. ITPtambién participa en la segunda fase de Clean Sky con la categoría de socio principal, reservada para los que están en el núcleo del proyecto. Según comentan desde la firma con sede en Zamudio (Bizkaia), es el mayor esfuerzo en I+D+i de la empresa vasca, que tiene más de 25 años de trayectoria industrial.
Clean Sky aspira a una reducción de emisiones de CO2 del 30%. En el caso del impacto sonoro, busca un recorte de hasta el 75%. Las investigaciones durarán hasta 2022.
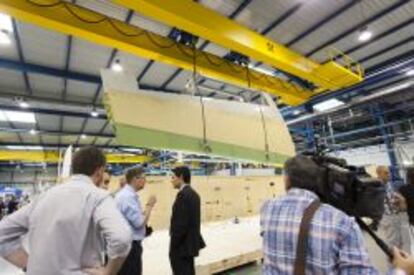
El constructor aeronáutico Airbus ha distinguido a su proveedor Aernnova por su “excelencia operativa”. El grupo europeo le ha otorgado el premio Best Performer Award 2016 en la categoría de estructuras aeronáuticas y materiales.
Según Airbus, el galardón “reconoce a Aernnova por su rendimiento excepcional, poniendo en valor su ingeniería de primer nivel, las capacidades industriales y la calidad de sus productos y servicios, así como la larga trayectoria como socio y suministrador preferente”. Airbus también ha valorado “las entregas en fecha, una cultura de mejora continua y una fuerte ética en los negocios”. Antes de este premio, Aernnova también había sido distinguida por Airbus como Miembro Acreditado, dentro del Programa SQIP en 2015, por “su liderazgo y experiencia en el mercado de aeroestructuras”.
El Best Performer Award 2016 fue entregado por Klaus Richter, uno de los principales ejecutivos de Airbus, en una ceremonia en la ciudad alemana de Hamburgo. Al evento, denominado Conferencia Global de Proveedores, acudió Iñaki López Gandásegui, presidente y consejero delegado de Aernnova. En el acto, el directivo vasco declaró que “estamos encantados y muy orgullosos de recibir este prestigioso premio de Airbus. Aernnova es desde hace tiempo su socio preferente, tras demostrar su compromiso con la excelencia en el desempeño operacional, competitividad a largo plazo, flexibilidad, anticipación e innovación”.
Aernnova, especializada en estructuras aeronáuticas, facturó más de 600 millones el año pasado con 4.300 empleados. Con plantas en España, está presente en México, Estados Unidos, Brasil y Rumanía.