La apuesta de Renault por el vertido cero en Tánger
La fábrica en Marruecos del grupo automovilístico francés logra reducir un 98% el CO2.
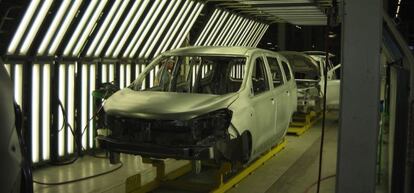
Conforme pasan los años, los coches son menos y menos contaminantes porque los fabricantes han desplegado todos sus conocimientos y experiencia en este terreno. Pero ¿qué hay del proceso de fabricación? Renault, con su planta de Tánger, parece haber aceptado el reto.
La planta tiene fama de ser la más grande de la región y también la más limpia, hazaña lograda con el grupo Veolia, que participó desde su concepción para evitar toda contaminación y hacer de Renault Melloussa una fábrica de “vertido cero”.
Una de las piezas clave del dispositivo es la caldera de biomasa. Según Veolia, representa un avance en materia de creación de energía térmica a partir de elementos naturales como la madera o incluso desechos de la industria agrícola.
El trabajo se lleva a cabo como en una sala de calderas tradicional, pero agregando una dosis de modernidad que permite mayor eficiencia y óptimo rendimiento en función del combustible utilizado, explican desde Veolia.
De ceniza a abono
Transportado por camiones de volteo que van y vienen sin cesar, el biocombustible llega a la fábrica y se almacena en silos. Después, la mezcla es homogeneizada y, de ahí, transferida a la caldera. Aunque podría parecer una labor sencilla, implica toda una serie de parámetros que exigen supervisión y minuciosos reglamentos para conseguir que al final de la combustión no queden más que cenizas. Estas, igual que las cenizas arrastradas por los gases de combustión, se recuperan para almacenarlas.
El grupo Veolia participó desde el inicio en la concepción de la planta
En la actualidad se estudia un proyecto de reutilización. Según Veolia, se trataría de hacer abono, en vista de que son ricas en elementos nutricionales.
Las calderas suministran agua a distintas temperaturas a los circuitos de agua caliente de la fábrica, en particular al departamento de pintura, que es un gran consumidor de energía. Hay instaladas dos calderas de seis megavatios, y está prevista una tercera para satisfacer las crecientes necesidades de energía.
Los resultados están a la altura de las expectativas. Las emisiones de dióxido de carbono se redujeron un 98%, el equivalente a evitar 135.000 toneladas de CO2 al año; para compensar las toneladas restantes, se procederá ya sea a comprar crédito de carbono o a producir energía renovable in situ.
Otro de los temas que atrae la atención se utiliza en circuito cerrado, un tratamiento digno de una planta depuradora con diversos recipientes a la medida de las necesidades de la unidad. Más adelante esta agua se filtra por medio de la técnica de ósmosis, que permite, al final del proceso, obtener un “agua industrial”, líquido puro en el sentido literal del término. Esta sirve para alimentar diversos procesos, como el tratamiento de las superficies de los autos y el pintado. El proyecto recibió en 2011 el premio de Energía Sostenible de la CE.