La demanda de turbinas más potentes deja sin opciones a Vestas en León
El mercado ha pasado de pedir modelos de dos a cuatro megavatios El aumento de los equipos complica el transporte y la instalación
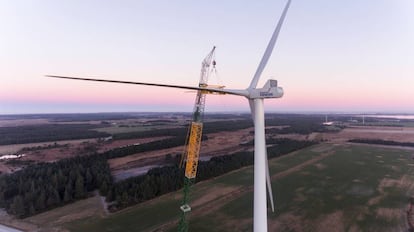
Vestas achaca el cierre de su planta de Villadangos del Páramo a la baja demanda de los aerogeneradores de 2 MW que son los que se fabricaban en el municipio leonés. Aunque dolorosa para las 360 familias que dependían de la fábrica, la decisión del grupo danés responde a la lógica del mercado.
La caída del coste de la energía eólica inducida por las subastas, el traslado de la inversión hacia emplazamientos de poco viento y la necesidad de torres más altas empuja a los fabricantes a desarrollar turbinas más potentes.
Según un informe publicado en septiembre por Wind Europe, la asociación europea de la industria, los motores de más de 4 MW, para eólica terrestre, y de más de 8 MW, para marina, se convertirán en la norma en los próximos cinco años.
“Los niveles de potencia de los aerogeneradores terrestres instalados se sitúan en los 2,5 MW, aunque las turbinas más demandadas ya cuentan con capacidades de entre los 3,5 y 4,5 MW”, confirma Antonio de la Torre, director de tecnología de Siemens Gamesa. “En el ámbito marino, los rotores son muy superiores y pueden alcanzar, en nuestro caso, los 8 MW”, añade.
De la Torre atribuye esta tendencia a los avances en nuevos materiales y tecnologías de control y logística, que han permitido reducir notablemente el precio mínimo al que se necesita vender la energía para garantizar la rentabilidad del parque durante toda su vida útil, parámetro conocido por los inversores como coste eléctrico nivelado (LCoE por sus siglas en inglés).
Los parques que utilizan rotores más potentes alcanzan su capacidad instalada con menos máquinas, lo que repercute en un menor LCoE para los promotores.
“Esto resulta particularmente importante en las instalaciones marinas, puesto que allí la complejidad de los proyectos es mayor”, precisa. Así, destaca que entre 2009 y 2015, el LCoE descendió alrededor de un 40% en la UE y la previsión es que siga bajando en los próximos años.
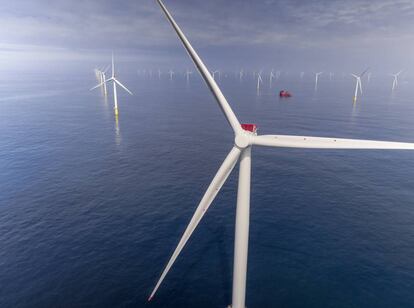
Abaratar los costes
Javier Nieto Calduch, responsable de offshore en la firma de ingeniería Esteyco, coincide en que las turbinas actualmente instaladas en alta mar no exceden de los 5-6 MW. Sin embargo, los proyectos en curso, que estarán operativos en el próximo lustro, contemplan motores de entre 8 y 12 MW. “El motivo, más o menos común a todas las regiones, es tratar de abaratar los costes por MW de construcción, instalación y operación”, afirma.
En el caso de la eólica terrestre, a la búsqueda de eficiencia se suma el factor tierra. Después de 20 años de crecimiento, las localizaciones más atractivas en cuanto a disponibilidad de recurso empiezan a saturarse. “Ahora los promotores eligen zonas donde el viento sopla menos y eso conlleva aumentar el tamaño de los rotores y la altura de las torres para capturar el mayor recurso posible”, explica Eneko Sanz, director general de Nabrawind Technologies.
Los promotores encargan rotores más grandes para abaratar los costes de construcción, montaje y operación
Vestas informa de que ha pasado de ofrecer aerogeneradores con una potencia máxima de 3 MW en 2008 a 4,2 este año, pero lo que más ha crecido es el tamaño de los rotores, cuya área de barrido ha pasado en el mismo periodo de 100 a 150 metros de diámetro, lo que les permite capturar mucho más viento.
“Cuando el nuevo producto no cabe en la fábrica –por tamaño, necesidad de utillaje y grúa o por volúmenes de producción–, los costes de adaptación de las fábricas son muy elevados y se debe estudiar en profundidad las ventajas e inconvenientes de producir localmente”, dice Federico Néstor González Vives, vicepresidente de tecnología de Vestas Mediterranean.
Recuerda que los mercados eólicos más pujantes, la mayoría de ellos ubicados en economías emergentes, están ofreciendo a los fabricantes ventajas retributivas o fiscales u obligándolos a producir localmente. “Si a eso le sumamos los costes de transporte y mano de obra que se requieren en mercados de crecimiento limitado, las oportunidades de readaptar fábricas se reducen”, subraya.
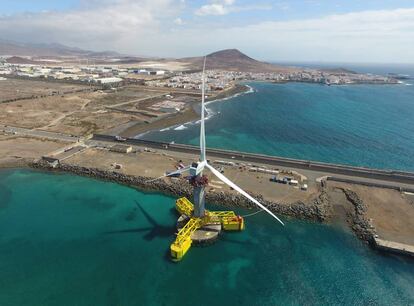
El aumento de tamaño de los componentes plantea también dificultades en el transporte y el montaje de los equipos. Empresas como Esteyco y Nabrawind han visto en estos retos una oportunidad de negocio.
“Al incrementarse el peso de las turbinas y la longitud de las palas –de 60 metros a más de 100 en offshore– se necesitan subestructuras más altas y fuertes para soportar las nuevas cargas y que los medios marinos evolucionen, pues no hay barcos y grúas capaces de manejar las dimensiones que están por venir”, explica Nieto Calduch, de Esteyco.
Consciente de que esto puede provocar un cuello de botella en el futuro inmediato, la consultora ha desarrollado un prototipo de torre de hormigón con una turbina de 5 MW, que puede llevarse flotando e instalarse sin necesidad de grandes buques grúa. El proyecto, Elican, se prueba a escala real en el puerto de Arinaga, en Canarias.
Para eólica terrestre, Nabrawind, firma con sede en Pamplona, ha patentado palas que pueden transportarse divididas en módulos y encajarse como si fueran bloques de Lego en el parque, y una torre tubular de acero autoizable que tampoco requiere grúas para el montaje. La compañía ha instalado el prototipo de su torre, Nabralift, en Eslava. Con 160 metros de altura, es la más alta del mundo, aunque es un 20% más liviana que las convencionales.
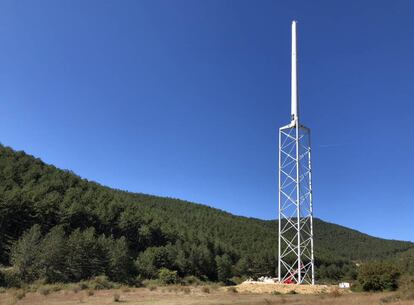