Renovarse para sobrevivir
El pinchazo de la burbuja inmobiliaria colocó al extremeño Grupo Herrrera al borde del cierre, pero encontró olvidada en un cajón una idea 'prefabricada' para renacer.
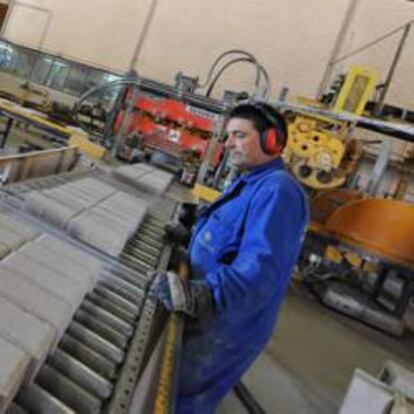
La crisis financiera, el pinchazo de la burbuja inmobiliaria, el deterioro de las perspectivas en la economía productiva... todos los pasos que han dado como resultado la situación actual fueron golpeando a la empresa extremeña Grupo Herrera, en todas y cada una de sus tres divisiones: calizas y áridos, fabricación de materiales de construcción y diseño y ejecución de instalaciones industriales prefabricadas.
Se llegó así a una situación límite en la pasada primavera: con menos encargos para su filial Hecoinsa (Herrera Construcciones Industriales), menor demanda de materiales, impagos y corte de las líneas de financiación, el grupo extremeño fundado hace cuatro décadas se vio abocado a la suspensión de pagos, y todo apuntaba a que seguiría el camino de otras firmas del ramo: concurso de acreedores, liquidación y cierre.
Fue entonces cuando Julián Herrera, presidente del grupo e hijo del fundador, decidió dar un golpe de timón y recuperar un proyecto que criaba polvo en un cajón: la construcción de viviendas prefabricadas, aprovechando su conocimiento de lo que se implantó hace mucho en Alemania, y con el respaldo de la maquinaria, tecnología y personal de Hecoinsa.
"Hasta entonces estábamos desbordados por los encargos de construcciones de tipo industrial y no podíamos distraer esfuerzos en el proyecto residencial, pero vi que había llegado el momento", explica.
Antes, Julián Herrera reunió a los principales acreedores y proveedores y puso las cartas sobre la mesa: o se liquidaba el grupo y cada cual cobraba lo que pudiera, o se le daba confianza para poner en marcha una línea en nuevos mercados. Su plan de viabilidad fue aceptado y Herrera no sólo salvó el match point, sino que ahora mira el futuro con optimismo y prevé que sus empresas saldrán reforzadas.
Menor coste
El plan supuso la adaptación de Hecoinsa para, aprovechando el sistema Betonhouse -muro multiuso prefabricado de doble pared-, poner en el mercado casas más baratas y construidas en menos tiempo. Con los ojos puestos en la VPO, pero sin descartar la vivienda libre, ya que el sistema permite todo tipo de construcción (aislada, adosada o en altura), Herrera contactó con los promotores para ofrecerles casas con menor coste en materiales y mano de obra pero que cumplen sobradamente las exigencias del nuevo Código Técnico de la Edificación en cuando a durabilidad (la vida útil supera con mucho el medio siglo) y aislamiento acústico y térmico.
La idea va calando, y el grupo ya tiene encargadas 800 viviendas y está a punto de firmar contratos con cooperativas de toda España para hacer 2.000 más. En teoría el sistema es simple: sobre el terreno se hacen los cimientos y el suelo, con anclajes para los muros. Mientras, en Hecoinsa (ubicada en Puebla de la Calzada, una pequeña población cercana a Mérida) se fabrican los muros (normalmente doble pared de siete centímetros de grosor por cada lado, de hormigón y con un forjado en medio), elementos de la cubierta, escaleras, losas para el suelo de los pisos superiores... Luego todo se traslada en camiones al sitio elegido, y personal especializado monta las paredes sobre los anclajes y se rellena el hueco del medio con hormigón, como un gigantesco Lego. De este modo, se ahorra tiempo (la casa se levanta en la mitad de tiempo que si se hiciese por el sistema convencional y los muros están listos para pintar directamente, sin tratamiento añadido), costes (hasta un 15% más baratos) y personal (cuatro operarios pueden montar una promoción de 15 viviendas en un mes). Además, hay mejoras añadidas como la seguridad -no hay que montar andamios-, la limpieza -se evitan los escombros- y la menor contaminación, ya que casi no hace falta maquinaria sobre el terreno.
Así, hacer una vivienda de 90 metros cuadrados sale por unos 72.000 euros, "y el ahorro se puede invertir en mejorar calidades en pavimentos, por ejemplo", explica Herrera, y agrega: "El coste de la estructura supone alrededor del 60% del total, así que un 15% es mucho". La aparente sencillez del sistema oculta un trabajo previo muy complejo. Herrera ha desarrollado un software propio, de manera que las casas se diseñan en tres dimensiones y si se intenta incorporar algún elemento inadecuado, el programa lo rechaza.
Concluido el diseño en el departamento técnico, se envía por fibra óptica la orden a la fábrica, donde robots también desarrollados por la firma eligen componentes, montan y ensamblan. Luego se carga en los camiones y se lleva a la promoción. Todo el personal se ha formado en Hecoinsa con lo que la coordinación y la profesionalidad está garantizada.
El éxito de la idea ha llevado al Grupo Herrera a establecer una alianza estratégica con la promotora Interdersur para dar un paso más: crear un modelo de utilidad que ya incorpore en la fase de prefabricado las preinstalaciones para agua, electricidad o aire acondicionado y calefacción.
También se piensa en nuevos mercados, y Herrera ha establecido contactos con países como Marruecos, donde se espera un boom de la construcción de viviendas protegidas, ya que se estima que hay un déficit de en torno a 800.000 casas de este tipo.
Una firma construida por un albañil
El germen del Grupo Herrera fue creado por Antonio Herrera, padre de su actual presidente. Antonio era albañil y aprovechó los momentos de parón en las obras por el mal tiempo para construir una máquina que fabricaba bloques para la construcción.Hoy, más de 40 años después, el Grupo Herrera cuenta con tres empresas Herrera 1 (la matriz, dedicada a fabricar ladrillos y pavimentos), Calizas y Derivados (para autoabastecimiento de materia prima, aunque también sirve a obras ajenas, como las del AVE Madrid-Lisboa) y Hecoinsa, de construcciones industriales y ahora dedicada a casas prefabricadas. Cuenta con 270 trabajadores, la mayor parte formados por la propia empresa para tareas de control de los procesos automatizados, y facturó en el último ejercicio 30 millones.Según explica Julián Herrera, la matriz no se llama Herrera 1 porque se pensase luego ir a Herrera 2, 3... "sino porque vimos que el nombre Herrera estaba cogido, y como queríamos mantener en la marca el apellido de mi padre, le pusimos el 1".El departamento de I+D del grupo se ha asociado con las principales firmas españolas de materiales de construcción para desarrollar el DB-Block, un nuevo ladrillo de aislamiento acústico que multiplica el efecto aislante, ahora en fase de desarrollo.
Apuesta por el negocio medioambiental
Una de las actividades más relevantes del Grupo Herrera es su trabajo en restauración medioambiental. Su encargo más sonado fue la rehabilitación del canal afectado por el desastre de Boliden en Aznalcóllar que afectó al entorno del parque de Doñana. Más recientemente, Herrera ha realizado el acondicionamiento de canales en el parque del río Guadaira, en Sevilla, que ocupa 54 hectáreas. Todos los elementos, como taludes, fondos antierosión, etcétera, se fabrican en la sede central y luego son transportados al lugar escogido para su montaje.Respecto a la división industrial, la firma extremeña fue la encargada de las nuevas instalaciones prefabricadas de la factoría de Heineken en Andalucía, cuya inversión rondó los 320 millones. También ha realizado el nuevo centro de Merkamueble, de 100.000 metros cuadrados, en la capital andaluza. Igualmente, todas las piezas de ambas instalaciones se fabricaron en Puebla de la Calzada y luego fueron montadas en un tiempo récord en sus ubicaciones.