La fábrica del futuro tiene un clon digital
Las empresas necesitarán contar con una factoría digital por cada centro de producción que posean si quiere seguir siendo competitivas
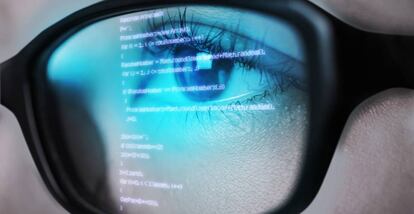
Actualmente, se habla mucho en el sector industrial de la llamada industria 4.0. Es como comúnmente se denomina la forma que adopta la industria tras la cuarta revolución industrial que ya estamos viviendo. Este nuevo cambio consiste principalmente en la creación de las llamadas smart factories o fábricas inteligentes gracias a la integración de nuevas tecnologías como la simulación. La principal ventaja de las fábricas inteligentes es que disponen de una mayor capacidad de adaptación ante las necesidades de los procesos de producción y una gestión mucho más eficiente de los recursos.
Según los resultados de una encuesta publicada recientemente por Gartner, el 48% de las empresas que ya se están dando cuenta de los beneficios de la internet de las cosas (IO) están utilizando o planean utilizar gemelos digitales a finales de este año. Y, al menos el 50% de las empresas manufactureras que cuentan con ingresos anuales de más de 5.000 millones de dólares planean iniciar al menos una iniciativa digital gemela para 2020.
Lo que esto significa es que cualquier compañía dedicada a la industria que quiera sobrevivir en el futuro necesitará una fábrica extra por cada otra que tenga. Sin embargo, esta fábrica extra no será física, sino digital. Pero, ¿qué es un gemelo digital? Es un modelo virtual simulado de un producto de trabajo real, informado por sensores montados en el producto físico que recopilan y envían datos operativos en tiempo real, del mundo real. Al estudiar el gemelo digital en condiciones reales de trabajo, las empresas pueden, por primera vez, analizar el producto en acción, a lo largo del tiempo, en su entorno operativo real.
Esta retroalimentación permite al equipo de desarrollo de productos cerrar el ciclo en sus simulaciones iniciales al revelar las fortalezas y debilidades del diseño en el campo. Los ingenieros pueden tomar decisiones más informadas para futuros diseños y mejorar la precisión de sus simulaciones. Y lo que es aún más importante, los gemelos digitales permiten por primera vez un verdadero mantenimiento predictivo. En lugar de realizar un mantenimiento excesivo o un mantenimiento excesivo de los productos para evitar costosos tiempos de inactividad, reparaciones o sustituciones, las empresas pueden actuar “justo a tiempo” para resolver cualquier problema de rendimiento del producto previsto por el gemelo digital.
Pueden visualizar exactamente cuándo y dónde se necesita mantenimiento en lugar de hacer conjeturas ciegas y apuestas seguras. El costoso tiempo de inactividad no planificado es reemplazado por un mantenimiento menos costoso durante las paradas programadas.
El ahorro de tiempo y de costes es considerable. Gracias al auge de la tecnología de productos conectados de forma inteligente, que permite el montaje de sensores duraderos a precios competitivos en máquinas y dispositivos en funcionamiento, el gemelo digital es una idea cuyo tiempo ha llegado claramente.
La simulación se lleva usando en el mundo digital para simular aspectos de la vida real prácticamente desde su incepción. Sin embargo, hemos avanzado mucho desde los tiempos en que los ordenadores se utilizaban para realizar simples cálculos matemáticos. La potencia y complejidad de los ordenadores y programas actuales les permite hacer simulaciones increíblemente complejas. Puede sonar a ciencia ficción, pero en la actualidad ya existen programas capaces de simular procesos industriales de principio a fin con gran exactitud.
Uno de los mayores costes que sufren las fábricas se da cuando se requiere introducir un ajuste o novedad en el proceso de fabricación. Por ejemplo, una situación muy típica en la que esto ocurre es durante el diseño de una nueva pieza para una máquina. Ninguna pieza sale bien al principio. Es más, hay que seguir un largo y costoso proceso de ensayo y error hasta que se obtiene la pieza perfecta.
Con la fábrica digital se puede simular todo sin coste alguno y muchísimo más rápido. Gracias a su avanzada tecnología, la simulación es capaz de detectar en tiempo real todos fallos que surgen durante el proceso, por muy pequeños que sean, y corregirlos al momento. Incluso pueden ofrecer sugerencias sobre cómo mejorar el producto.
El software de mantenimiento predictivo facilita y agiliza el desarrollo de ese primer gemelo digital. Cuando se combina con otras herramientas de desarrollo de software, puede crear rápidamente un modelo de sistema –un gemelo digital– del producto. Una vez conectado, el gemelo digital puede utilizar el estado actual del producto para simular estados futuros, permitiéndole predecir cuándo pueden ocurrir problemas e incluso utilizar estas predicciones para programar el mantenimiento del producto físico.
Por último, hay que pensar también en las ventajas que ofrece la simulación aparte de una reducción de costes. Puede suponer una herramienta muy importante a la hora de mejorar la seguridad laboral. Las fábricas, aunque sigan todos los protocolos de seguridad, no están libres de peligros, algo que con la simulación digital del proceso se puede afrontar sin comprometer la seguridad de los trabajadores.
Los simuladores no son perfectos, pero el ritmo al que siguen mejorando es prácticamente diario. Las empresas se están dando cuenta de la necesidad de esta otra fábrica digital, ya que un espacio virtual en el que poder experimentar sin preocuparse por los costes o el tiempo ofrece demasiadas ventajas como para ignorarlo. Por eso la industria del futuro necesitará de dos fábricas si espera seguir siendo competitiva.
Gilles Lebiez es Managing Director Iberia en ANSYS