Tecnalia lleva los sensores al metal, los puentes y el mar abierto
La investigación del centro en el área de industria 4.0 crece un 30% Indaga en sistemas para componentes metálicos, energía y construcción
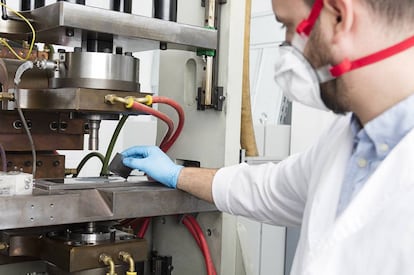
Un fabricante de componentes metálicos prueba un nuevo sistema de sinterización en Barcelona. En el golfo de Bizkaia, un grupo de 11 empresas pone a flotar sus piezas en una enorme boya para ver cómo responden a la presión de las olas y el viento. En Derio (Bizkaia), ingenieros han reducido a escala un puente ferroviario de Alicante para encontrar nuevas formas de prevenir daños en la estructura real.
En los tres proyectos intervienen algoritmos, sensores y robots, lo cual es una muestra del creciente interés de las empresas por aprovechar nuevas tecnologías que faciliten sus procesos productivos. Tecnalia, fundación con sede en San Sebastián que lidera los tres experimentos, puede dar fe de ello.
En el último año, ha visto multiplicarse su actividad investigadora en temas de industria 4.0 (robótica, automatización, realidad aumentada) en más de un 30%, tanto en ingresos como en número de acuerdos.
“Colaboramos con un centenar de empresas industriales, el 70% de ellas pymes, en proyectos de transformación digital que han supuesto para nosotros una facturación de 50 millones en los dos últimos años”, informan desde el centro de investigación.
La mayoría de esos proyectos indagan en la aplicación de nuevas tecnologías, principalmente en los sectores de manufactura, energía y construcción.
Sinterizar en 10 segundos
Ames es una compañía con más de 60 años de actividad que fabrica piezas metálicas para componentes de automoción (los engranajes de las cajas de cambio o las válvulas de las bombas de aceite, por ejemplo) en su planta de Barcelona (aunque tiene otras tres en Hungría, Estados Unidos y China).
Para obtener las piezas, Ames calienta polvo metálico prensado en hornos eléctricos que alcanzan temperaturas lo suficientemente altas como para que se formen puntos de soldadura entre los granos sin que se llegue a fundir el hierro. Este proceso, que se conoce como sinterización, es largo (puede llevar 24 horas) y demasiado costoso si lo que se quiere producir son pequeñas cantidades.
Por eso, Ames, en consorcio con otras cinco empresas, entre ellas Airbus y Kyocera, prueba un nuevo sistema desarrollado por Tecnalia y la Universidad de Sevilla que sustituye los hornos por una fuerte descarga eléctrica durante la fase de prensado. El ciclo entero se reduce a 10 segundos, se evitan gases contaminantes y consigue un ahorro en costes de hasta el 20%.
“No hemos podido probar las piezas obtenidas así a nivel industrial, pero en el laboratorio hemos constatado que su desgaste es bastante inferior al de las piezas hechas de la manera tradicional”, dice David López Gascón, investigador de Ames, que aplicará el método solo para la producción de series cortas.
Un laboratorio flotante
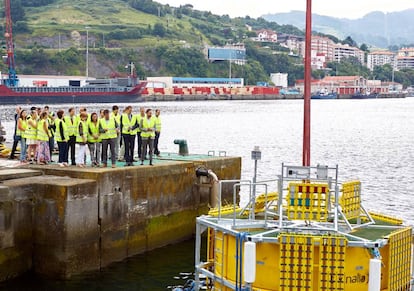
La búsqueda de espacio para rotores más grandes y la caída de los costes de producción están poblando los mares europeos de aerogeneradores. El auge de la eólica offshore es una oportunidad para fabricantes de estructuras metálicas, líneas de amarre, sistemas de manipulación y fondeo, revestimientos, tuberías y pernos. Todas estas empresas se enfrentan al mismo problema: la corrosión provocada por el agua de mar.
En busca de soluciones, un consorcio de 11 compañías vascas ha puesto en marcha HarshLab, un laboratorio flotante a 1.700 metros de la costa vizcaína, para ensayar y validar sus productos en un entorno hostil. La estructura, que tiene el aspecto de una boya, opera en mar abierto, en un área acotada frente al puerto de Armintza, en Bizkaia. El proyecto cuesta 700.000 euros y es financiado por las firmas participantes, el Gobierno vasco y Tecnalia.
Sensores en el puente
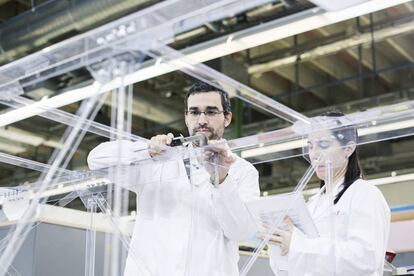
El derrumbe del puente Morandi, en Génova, se podría haber evitado si el operador de la infraestructura hubiese detectado a tiempo el agrietamiento del hormigón. En Derio, ingenieros de Tecnalia trabajan en el desarrollo de un sistema de monitorización basado en sensores que, en caso de notar cualquier anomalía en los materiales de un puente, envía una alerta a la empresa responsable.
Para probar el sistema en un laboratorio, han encogido en 150 veces el puente Barranco de Aguas de Alicante, utilizando un modelo a escala hecho en policarbonato. Las firmas andaluzas Cemosa (sensores) y Magtel (algoritmos) colaboran con el proyecto, presupuestado en 6,4 millones de euros, de los cuales 4,8 son financiados por el CDTI.
Colaboración con empresas
Surgida en 2011 como resultado de la fusión de ocho centros de investigación vascos, Tecnalia facturó el año pasado 103,9 millones de euros y tiene 1.445 empleados. La mitad de sus ingresos provienen de contratos de colaboración con empresas en proyectos de I+D, que el año pasado aumentaron más de un 40%.
Por la venta de derechos de propiedad industrial, la corporación tecnológica obtuvo en 2017 unos ingresos de 3,2 millones de euros. Tecnalia es la segunda organización española con mayor número de patentes europeas, con 555 en cartera.