Revolución orgánica en las cadenas de montaje
Ecología en su máxima expresión. El coche del futuro se fabrica con materiales reutilizables y totalmente naturales que, además, provienen de la agricultura y aportan la misma seguridad
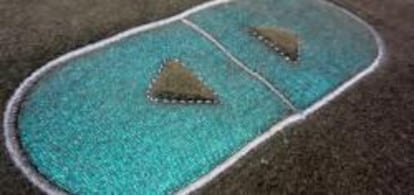
Parece ciencia ficción, pero no lo es. La industria de la automoción da la bienvenida a una nueva forma de fabricación de componentes. Los materiales de origen agrícola irrumpen en el sector: se siembran, se riegan, crecen en el campo, se recolectan y sirven, entre otras cosas, para fabricar todo tipo de piezas de automóvil. Y eso que llevan entre nosotros toda la vida. La diferencia es que ahora se saben utilizar.
Al margen de las otras fórmulas para fabricar coches verdes (considérense los avances en propulsión eléctrica o híbrida), la UE exige que en 2015 el 95% de los materiales presentes en un coche sean reciclables. Para alcanzar esta cifra, es imprescindible comenzar a sustituir espumas, textiles sintéticos y plásticos, cuyas vidas terminaban, hasta ahora, en los desguaces. Sin embargo, esta política de materiales ecológicos ya se utiliza desde hace algunos años en modelos de alta gama y camiones fabricados por Volvo o la factoría de Mercedes en Brasil. Ahora en España se ha dado un paso más.
Recientemente, Fedit (la Federación Española de Centros Tecnológicos) ha presentado un estudio, salido del observatorio del sector de fabricantes de equipos y componentes de automoción -que incluye a todos los actores de la industria-, donde se pone de manifiesto que estos biomateriales aplicados en automoción "poseen una excelente capacidad de reciclaje" y son ideales para cumplir con las exigencias europeas. Por ello, los centros de I+D se han puesto a trabajar.
El primer paso se ha dado con el desarrollo de paneles y otras piezas para el interior del coche a partir de fibras naturales como el lino, el cáñamo o el yute. Esta novedad, además de reducir el uso de derivados del petróleo, tiene otras ventajas frente a los tradicionales materiales sintéticos, ya que proceden de fuentes renovables que no escasean y son baratos; tienen un peso ligero, son biodegradables, no afectan a los procesos de fabricación y no producen alergias.
Asimismo, el estudio de Fedit resalta que los componentes naturales funcionan a la perfección en la automoción y son excelentes aislantes acústicos y térmicos. El coste de producción es mucho menor y durante su manipulación se reducen, notablemente, las emisiones de CO2. Todas estas cualidades hacen que, precisamente en nuestro país, se esté investigando sobre su uso para poder trasladarlo al mercado.
Un buen ejemplo de ello está en el centro de investigación y desarrollo Cetemmsa, situado en Mataró (Barcelona) y perteneciente a Fedit. Allí se trabaja en estos momentos en el desarrollo de un tejido idóneo para revestir los salpicaderos y las puertas de los vehículos. Este componente se basa en la eliminación de piezas de plástico (como los mandos o los elevalunas) e integra los múltiples botones de un coche en una sola pieza de tela. Gracias a esto se consigue un vehículo más ecológico, realizado con materiales reutilizables y que prescinde, casi por completo, del plástico.
Las otras posibilidades residen en el empleo de sustancias de origen vegetal, como las resinas procedentes de la soja, que se utilizan en la fabricación de pintura para coches. Igualmente, el almidón es una sustancia ideal en la fabricación de neumáticos, sin olvidarse de los lubricantes a base de aceites vegetales.
Gracias a la fibra de coco y el sisal se realizan rellenos de asientos y tapicerías más ecológicas. Son resistentes al fuego, impermeables y no desprenden vapores tóxicos cuando se calientan. Desde hace varios años, la planta de Mercedes Benz en Brasil fabrica los rellenos de asientos y reposacabezas de sus camiones con estos materiales, que también son transpirables. La casa alemana cuenta para ello con el trabajo de pequeños productores de la ciudad de Belém (Brasil).
Es indudable que, además de ser un beneficio medioambiental, la incursión de estos materiales en la fabricación de componentes contribuirá al desarrollo económico de las regiones agrarias más desfavorecidas de (entre otros lugares) Latinoamérica y Asia.
Mientras, en nuestro país, el primer prototipo de auto de Fórmula 3 fabricado con vegetales (zanahoria, soja, patatas y yute, entre otros), en sustitución de la fibra de carbono, ya se ha puesto en marcha. El vehículo está desarrollado por el Instituto Tecnológico del Plástico (Aimplas) en colaboración con la Universidad de Warwick (Reino Unido). José Antonio Costa, director gerente del centro, asegura que estos proyectos "resultan fundamentales para crear nuevos nichos de mercado respetuosos con el medio ambiente". Más en tiempos de crisis.
La cifra
95% de los componentes de un coche debe ser reciclable en 2015. La clave para lograrlo está en los textiles y las espumas.
Del campo directo a la fábrica
Cada año se cosechan en el mundo cerca de 35 millones de toneladas de fibras naturales extraídas de una amplia gama de plantas y también de animales. La búsqueda de nuevos mercados y usos es una buena noticia para el sector agrícola y ganadero. Además, se da por supuesto que la llegada de estos materiales a la automoción contentará también a los grupos ecologistas.Y eso que el uso de fibras naturales no es una novedad: a comienzos del siglo XX, en los albores de la automoción, Henry Ford utilizó pasta de soja para la fabricación de pomos de la palanca de cambios y gluten de trigo en las carcasas de las bobinas de sus vehículos.Enrique Díaz, responsable de composites de Aimplas (Instituto Tecnológico del Plástico), explica que las investigaciones en este ámbito se centran en "aprovechar materias primas provenientes de fuentes renovables, así como reducir drásticamente el consumo energético necesario para la fabricación de dichos composites". Por ello, los avances en los últimos años son prometedores.Se está investigando con distintas técnicas que van desde la modificación genética de los cultivos hasta el tratamiento superficial de las fibras. Todo lo necesario para adaptar estos cultivos a la fabricación de nuevos materiales y, por ende, poder trasladarlo al sector de la automoción.El reto también está en lograr que los biomateriales pasen todos los controles de validación (seguridad, vibraciones, estabilidad). El Centro Tecnológico de la Automoción de Galicia (CTAG) es el epicentro de un nuevo proyecto europeo encargado de llevar a la vida real, en un plazo máximo de cuatro años, estos avances.