Los barcos del futuro saldrán de una impresora
Navantia y la Universidad de Cádiz trabajan en el Astillero 4.0 El modelo contempla 13 tecnologías y la fabricación aditiva es de las principales

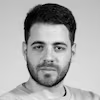
La robótica, domótica, realidad aumentada, impresión 3D y otras técnicas novedosas han trastocado en los últimos años gran cantidad de industrias. Sin embargo, algunas de gran peso, como la naval, parecen haber estado en la sombra, esperando el momento oportuno para sumarse a la carrera. Hasta ahora. En España, ha sido Navantia la que se ha puesto a la cabeza, contratando a diferentes entidades, como la Universidad de Cádiz, con el fin de transformar por completo los procesos de producción y fabricación. El objetivo final es el Astillero 4.0, un proyecto que comenzó a fraguarse en 2015 y que ya empieza a dar los primeros resultados.
“El sector naval tiene carácter global y atraviesa un momento de muy dura competencia. Los principales competidores ya están inmersos en procesos de digitalización”, explica uno de los expertos de Navantia que capitanea esta iniciativa. Por eso, prosigue, en este contexto la transformación digital es irrenunciable para asegurar la competitividad, sostenibilidad y mejorar la cuenta de resultados. Así, el modelo Astillero 4.0 contempla incorporar 13 tipos de tecnología: robótica industrial, fabricación aditiva, materiales avanzados, vehículos autónomos, dispositivos IoT, modelizado y simulación, realidad virtual y aumentada, big data, inteligencia artificial, plataformas digitales, nube, ciberseguridad y blockchain. “El acierto es encontrar la combinación de las mismas y las oportunidades que proporcionen mayor impacto, así como conseguir una velocidad que logre una implementación efectiva”, añade el profesional de la compañía naval.
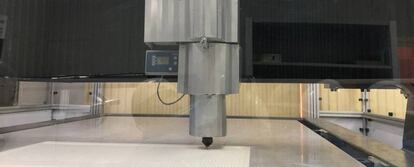
El plan, que comenzó hace algo más de dos años, ha tardado en mostrar sus primeras conclusiones debido, precisamente, a la complejidad que conlleva combinar todos estos trabajos en un mismo diseño. Una de las principales ramas, la de la fabricación aditiva o impresión 3D, es la que más frutos palpables ha obtenido. Uno de los que trabajan en esta línea, en las instalaciones de Puerto Real, es Sergio Molina, catedrático por la Universidad de Cádiz: “El proyecto pionero y que ya hemos terminado es 3DCabins, un rediseño de las cabinas de los buques y de los materiales con los que se construyen los camarotes de los barcos”. El otro ha sido Adibuque, por el que los expertos han realizado diferentes pruebas para ver qué tipo de mejoras ofrece la impresión 3D frente a la fabricación más tradicional. El resultado, hasta la fecha, ha sido la impresión de rejillas de ventilación para los barcos, “algo que ha sido un hito, porque no se había hecho antes”, apunta.
A partir de aquí, el objetivo es lanzar más proyectos, que a priori verán la luz en los próximos meses, con el fin de fabricar mediante estos procesos de impresión estructuras y elementos de más envergadura para los buques, así como ampliar la gama de materiales utilizados, ya que ahora todo está muy centrado en los polímeros. “Todas estas técnicas reducen costes, pesos y riesgos, además de facilitar los procesos. Aún estamos en una fase embrionaria, pero los primeros resultados son prometedores”, cuenta Molina.
El plan, además, no tiene impacto únicamente en el producto final. Va más allá de las diferentes piezas y materiales que conforman las naves. Como explican desde Navantia, las oportunidades tienen alcance en muchas dimensiones, “como el buque inteligente, llevando a nuevas cotas su operación y sostenimiento; la fábrica inteligente, flexible y adaptativa; las operaciones que integran la cadena de suministro de los programas y el trabajador conectado y programado”, relata el experto de Navantia.
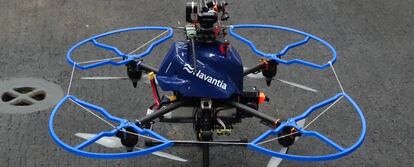
Por eso, y aunque la transformación es lenta y conviene ir paso a paso, “no hay producto que a priori haya de quedarse al margen de recoger los beneficios de la digitalización”, avanza el citado experto, siempre y cuando “se desarrolle la capacidad para incorporar de manera robusta y fiable las soluciones digitales a lo largo de la vida de los programas navales, bien sea en el proceso productivo o en el propio producto”, recuerda. Por ahora, lo más probable es que el primer programa que se beneficie de esta transformación desde las primeras etapas de la construcción sea el de las fragatas F-110 que previsiblemente encargará el Ministerio de Defensa, cuentan desde la empresa.
Sea como sea, los avances potenciales en esta materia son realmente grandes. Como recuerda Sergio Molina, la fabricación aditiva en el sector naval hace cosa de tres o cuatro años era prácticamente nula. “Cuando empezamos, hace dos años, salvo en algunas partes de Estados Unidos y del norte de Europa, no había nada, y en este tiempo ha habido un crecimiento bestial”. Además, añade, estas técnicas no van a desplazar a los profesionales del sector, sino que darán paso a una construcción y trabajo híbridos.
Sobre la firma
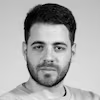